Researchers within the fields of supplies science and microelectronics are searching for sustainable methods to fulfill the world’s demand for pc energy. This may be achieved by creating microelectronics that function at a lot decrease voltages and require much less power. Therefore, thin-film alternate options to digital parts are a lot wanted.
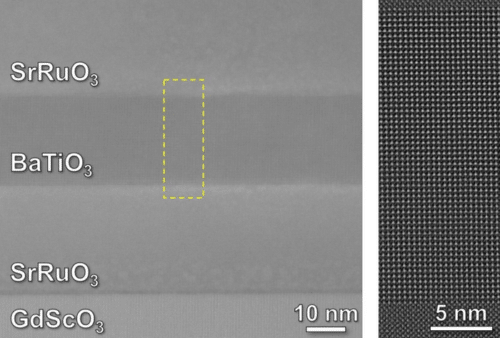
A bunch of researchers from Berkeley Lab and UC Berkeley have now found one energy-efficient methodology, which entails making a thin-layer model of a widely known materials with the exact qualities required for next-generation units.
Barium titanate (BaTiO3), which was first found greater than 80 years in the past, is utilized in a wide range of capacitors for digital circuits, ultrasonic mills, transducers, and even sonar. The scientists discovered a way to make BaTiO3 movies which can be solely 25 nanometers thick, or lower than a thousandth of the breadth of a human hair. Their polarisation, or the orientation of charged atoms, shifts as swiftly and successfully as within the bulk type.
“We’ve recognized about BaTiO3 for the higher a part of a century and we’ve recognized learn how to make skinny movies of this materials for over 40 years. However till now, no person might make a movie that would get near the construction or efficiency that might be achieved in bulk,” stated Lane Martin, a school scientist within the Supplies Sciences Division (MSD) at Berkeley Lab and professor of supplies science and engineering at UC Berkeley who led the work.
The researchers used a way often called pulsed-laser deposition to higher perceive what it takes to create the very best, low-defect BaTiO3 skinny movies. BaTiO3 is a ceramic substance that transforms right into a plasma when an intense ultraviolet laser beam is directed at it. The plasma then transmits atoms from the goal onto a floor to create the movie. “It’s a flexible instrument the place we are able to tweak a number of knobs within the movie’s development and see that are most essential for controlling the properties,” stated Martin.
The researchers found a model that intently reproduced a really slender slice of the majority by slicing every deposited pattern in half and analysing its construction atom by atom. Lastly, Martin and his staff produced small capacitors by sandwiching a movie of BaTiO3 between two steel layers.